Research & Development
His aim was to reduce the effects of humming, whirring, grinding and rattling, parasitic acoustic phenomena called NVH, in transmissions. A successful bet!
This determination to innovate has been an integral part of the DNA of each of the SUB-ALLIANCE member companies ever since.
" Alone we go faster, Together we go farther "
Combining our research and development capabilities and our know-how allows us to create and put this collective intelligence to work for you.
And allows us today to provide you with solutions of :
- Improvement of the global performances
- Weight reduction of products: for example PEEK, carbon fiber...
- Reduction of manufacturing costs
- The most demanding thermal management: alloys produced by casting metals, ceramics and powders
- Optimization and simulation of transmissions
- Optimization of the choice of materials according to their applications: computer simulation of material properties under stress
This approach allows us to manufacture the lightest products with extremely durable properties.
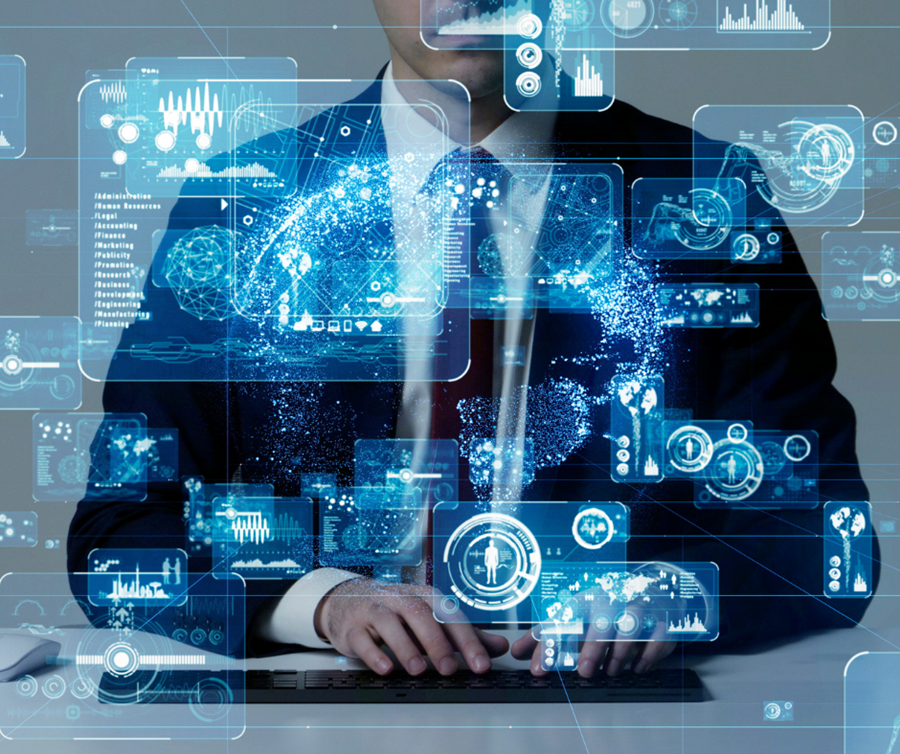
Research
- New advanced alloy materials for thermal management applications
- Increased production rate
- Decrease in production cost
- Reduced weight of composite parts
- Optimization of transmissions and gears through finite element simulations
Development
- Lightweight thermoplastic composite components for aircraft (weight, cost and CO2 reduction)
- High temperature composites for LEAP aircraft engines
- Transmissions for autonomous E-Drive vehicles (electric)
- High torque differential for racing vehicles
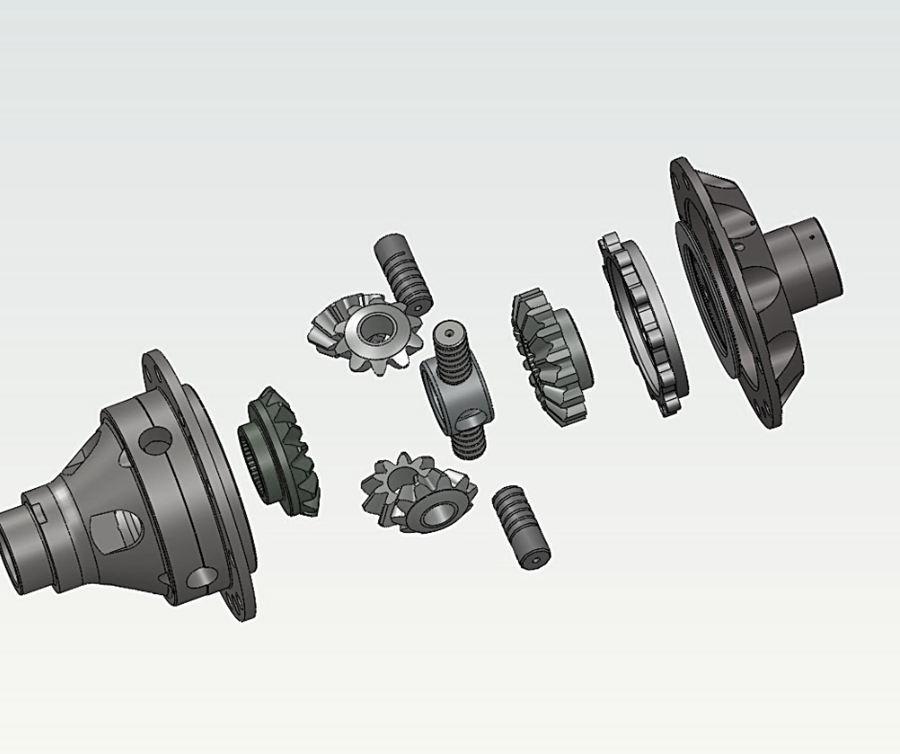
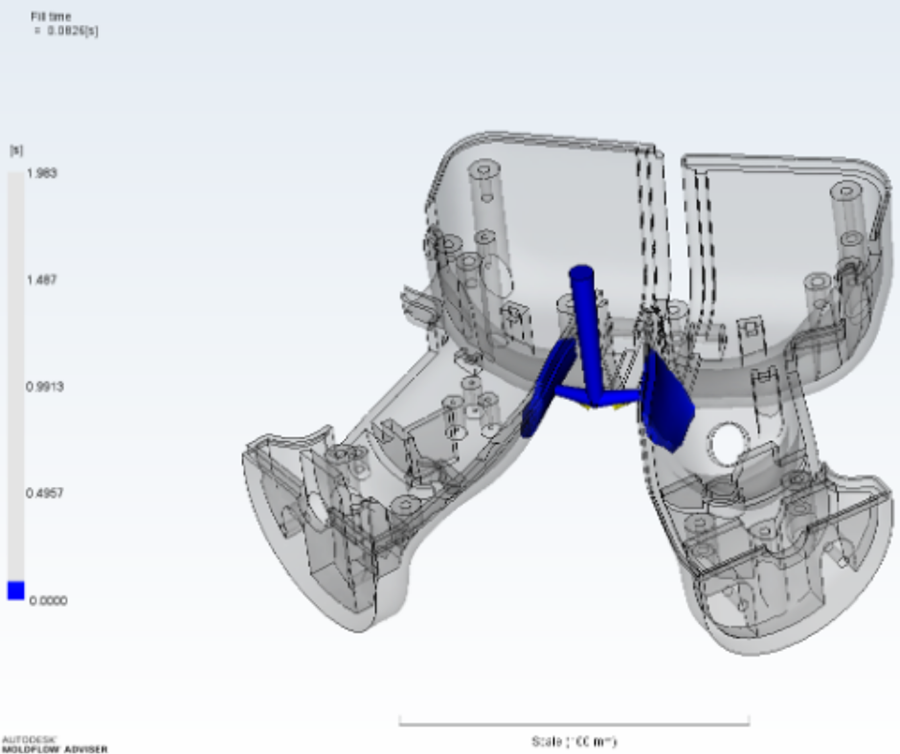
Design
We are at the forefront of software in their category so our development team will support you in your projects with a design & cost approach. We will be able to reduce weight, cost and increase production rates. With over 70 years of experience, we are able to work on any type of product regardless of its complexity.
Co-engineering
SUB-ALLIANCE is your ideal partner for developing and manufacturing advanced subsystems and components. With our co-engineering approach, we put our expertise at the service of your projects and are able to develop lighter, more robust and more cost-effective products.
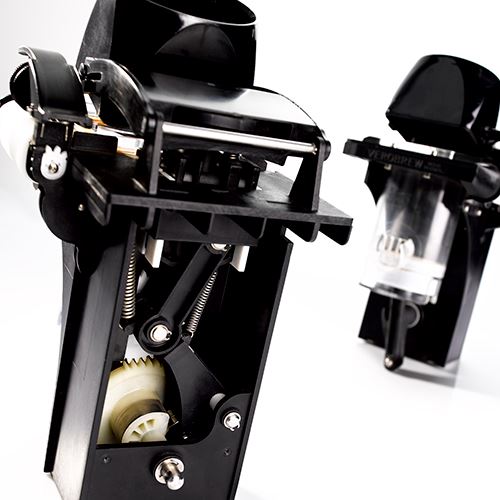